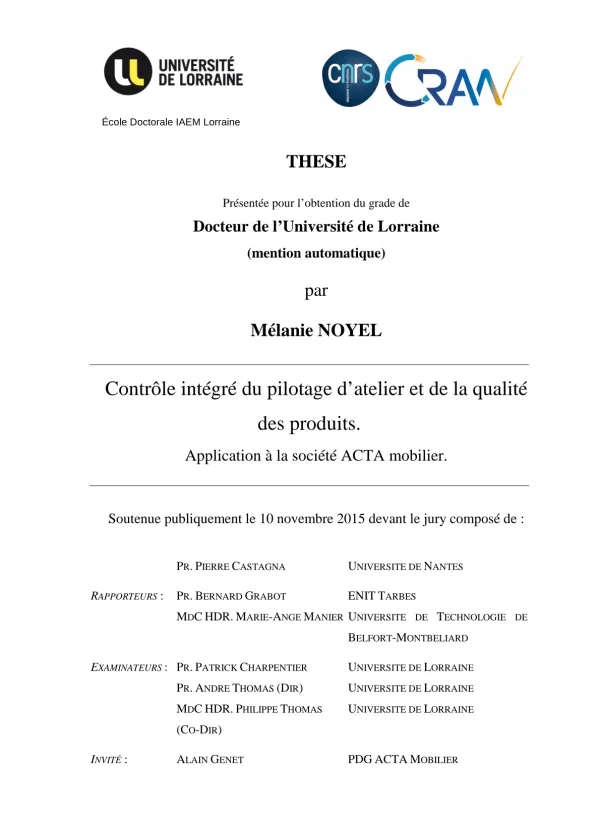
Contrôle Intégré du Pilotage d'Atelier et de la Qualité des Produits
Informations sur le document
Langue | French |
Format | |
Taille | 3.09 MB |
- Thèse
- Contrôle intégré
- Système d'information
Résumé
I.Contexte Industriel et Problématique chez Acta Mobilier
Cette thèse CIFRE, menée en collaboration entre Acta-Mobilier, fabricant de façades laquées haut de gamme situé près d'Auxerre, et le Centre de Recherche en Automatique de Nancy (CRAN), traite des problèmes de gestion de production et de maîtrise de la qualité. Acta-Mobilier, leader français du laquage haut de gamme pour des clients prestigieux tels que Schmidt et Mobalpa, souffre de boucles de production, d'un taux de reprise (non-qualité) important, entraînant des délais non respectés, des charges de travail instables et des pertes de pièces. L'objectif est d'améliorer la réactivité et l'efficacité de la chaîne de production, notamment en utilisant des systèmes contrôlés par le produit (SCP) et des technologies d'identification, comme la RFID, pour une meilleure traçabilité. Le MDF de 19 mm est le principal matériau utilisé.
1. Présentation d Acta Mobilier et de sa problématique
Acta-Mobilier, entreprise située près d'Auxerre, est spécialisée dans le laquage haut de gamme de façades pour l'agencement de stands, magasins, hôtels, cuisines et bureaux. Elle se positionne comme leader français sur ce marché de la co-traitance, travaillant avec des grands noms comme Schmidt, Mobalpa, et Lapeyre. Malgré son succès et une culture d'entreprise axée sur la valorisation humaine et l'amélioration continue, Acta-Mobilier rencontre des difficultés liées à la gestion de sa production. Ces difficultés incluent un taux de reprises (non-qualité) significatif, des délais de livraison non respectés, et des charges de travail instables. La non-anticipation de la charge conduit à une flexibilité forcée du personnel. L'entreprise essaie de maintenir une avance de deux jours sur les dates d'expédition pour pallier les retards potentiels, mais cela reste insuffisant. Une analyse révèle que le temps de transformation réel des pièces est très faible (0,4%) par rapport au temps total passé en production, le séchage représentant jusqu'à 50% de ce temps. Ces problèmes impactent fortement l'efficacité globale et nécessitent une intervention pour optimiser les processus.
2. Les Boucles de Production et leurs Conséquences
L'organisation de la production chez Acta-Mobilier présente une particularité: l'existence de boucles de retour de flux dans les différents ateliers (usinage, préparation, laquage). Ces boucles sont dues à la nécessité de traiter les deux faces des pièces (et parfois les chants), nécessitant des opérations répétées (apprêtage, séchage, etc.). La présence de ces boucles, inévitables sans investissement majeur dans la duplication des postes de travail, perturbe le flux de production et complexifie la planification. Le système FIFO (First In, First Out) souhaité par l'entreprise est constamment perturbé par ces boucles. De plus, l'existence de « circuits courts » (CC) pour les pièces perdues, abîmées ou nécessitant des modifications de dernière minute, amplifie la complexité de gestion et rend la planification encore plus imprévisible. Ces interruptions et reprises (rework) constantes engendrent des pertes de produits, empêchant la livraison complète des commandes, et constituent un frein majeur à l'efficacité de la production. La maîtrise de ces boucles et la réduction du taux de reprise sont donc des défis importants pour l'entreprise.
3. L Importance de la Maîtrise de la Qualité et ses Défis
La maîtrise de la qualité est un enjeu crucial pour Acta-Mobilier. Bien que l'entreprise priorise le traitement des pièces défectueuses, assurant un taux de service remarquable malgré le fort pourcentage de pièces à réparer, ces traitements au cas par cas provoquent des pertes de pièces et compromettent la livraison complète des commandes. La thèse explore comment améliorer le contrôle qualité sur des processus de fabrication instables. La méthode Taguchi's Quality Engineering (TQE) est présentée comme une approche proactive pour anticiper la qualité, mais ses limites (coût, non-réactivité) sont également soulignées. L'objectif est d'améliorer la prévision et la gestion des défauts, en comprenant les interactions complexes entre les différents paramètres de production et les causes des non-conformités. Le traitement prioritaire des pièces défectueuses, bien que garantissant un bon taux de service, est source de pertes et de retards; l'étude vise donc à optimiser ce processus pour éviter les pertes de pièces et améliorer la prévisibilité du respect des délais.
II.Amélioration de la Réactivité et de la Qualité
Pour améliorer la réactivité face aux variations de la demande et aux problèmes de qualité, la thèse explore plusieurs pistes. L'optimisation de l'ordonnancement est envisagée, en comparant des règles classiques comme FIFO, SPT, et EDD. Pour l'anticipation de la non-qualité, la méthode Taguchi et les réseaux de neurones sont étudiés, permettant de prédire l'apparition de défauts (coulures, etc.) en fonction de paramètres comme le grammage, la température et le temps de séchage. L'utilisation de cartes de contrôle permet un suivi dynamique et un réapprentissage en ligne des modèles de prévision pour s'adapter aux dérives du système de production. Un nouvel indicateur, le Ratio d'Opérations (RO), est proposé pour évaluer l'efficacité des réparations.
1. Amélioration de la Réactivité Décision Juste à Temps
Le manque de réactivité face aux événements imprévus (variations de stock, absences, pannes) nécessite une meilleure adaptation du planning de production. Pour y remédier, l’implémentation d’un système d’aide à la décision en temps réel est envisagée. Ce système fournirait à l’opérateur des informations reflétant la situation actuelle de la production et lui proposerait les meilleures alternatives possibles. L’objectif est de permettre une « décision juste à temps », c’est-à-dire d’adapter le planning au fur et à mesure des événements, afin de réagir efficacement aux imprévus et éviter les retards. L'opérateur, au cœur du processus, devient un acteur clé dans la prise de décision, permettant une plus grande flexibilité face aux changements. Ce système permettrait de répondre plus efficacement aux besoins changeants de production et optimiser le temps de réaction face aux aléas.
2. Maîtrise de la Qualité Prévention et Réaction
La thèse explore des méthodes pour améliorer la qualité et réduire le taux de reprises. Un axe principal consiste à agir directement sur la qualité des produits afin de diminuer le nombre de réparations et les perturbations associées. Le traitement prioritaire des pièces défectueuses assure un bon taux de service, mais engendre des pertes qui empêchent la livraison complète des commandes. L'étude examine des méthodes de maîtrise de la qualité, tant réactives que proactives. La méthode Taguchi’s Quality Engineering (TQE) est étudiée pour son approche préventive, permettant un réglage optimal des paramètres influents sur la qualité avant même la production. Cependant, la non-réactivité de ces méthodes face aux évolutions du système est un inconvénient majeur, mettant en avant l'intérêt des méthodes 'on-line' pour un suivi dynamique et une réadaptation automatique. La recherche d'un équilibre entre optimalité et robustesse face aux changements imprévisibles est un objectif principal.
3. Amélioration de la Qualité Prédiction et Réapprentissage
Pour prédire et limiter les défauts, des méthodes d'apprentissage automatique sont explorées. L'analyse porte sur l'utilisation de réseaux de neurones et d'ensembles de classificateurs pour la prévision de défauts. Des cartes de contrôle permettent un suivi dynamique du taux de mauvaises classifications, déclenchant un réapprentissage du modèle dès qu'une dérive est détectée. Ce réapprentissage en ligne permet d'adapter le système de prédiction aux évolutions du processus de fabrication et aux variations des paramètres influents (température, grammage, etc.). Un nouvel indicateur, le Ratio d'Opérations (RO), est proposé pour mesurer l'efficacité du processus de réparation et estimer l'impact des non-qualités sur le respect des délais. L'objectif est d'améliorer la prévision de la non-qualité et d'adapter le processus en temps réel pour maintenir le niveau de qualité souhaité.
III.Système Contrôlé par le Produit et Optimisation des Flux
Le cœur de la thèse repose sur l'implémentation d'un Système Contrôlé par le Produit (SCP). Au lieu de tracer chaque pièce individuellement, l'approche se concentre sur des containers intelligents, regroupant des pièces ayant la même gamme de fabrication. Ces containers, équipés de code-barres 2D, communiquent des informations cruciales (date de livraison, urgence, etc.) au système d'ordonnancement, permettant une meilleure synchronisation des flux. Un programme linéaire optimise l'ordonnancement, tandis qu'une cartographie visuelle en deux dimensions (utilisant des indicateurs clés de performance comme le nombre de retards et le taux de non-qualité) aide à la sélection de la règle de pilotage la plus adaptée (FIFO, SPT, EDD) selon l'état de saturation de l'atelier. L'objectif est de réduire le nombre de pièces en attente (WIP) et d'améliorer le respect des délais.
1. Systèmes Contrôlés par le Produit SCP Une Approche Décentralisée
La thèse explore l'implémentation de Systèmes Contrôlés par le Produit (SCP) pour améliorer la gestion des flux de production chez Acta-Mobilier. Contrairement aux systèmes de pilotage centralisés, les SCP distribuent la décision, en donnant un rôle actif au produit dans la synchronisation des échanges entre les différents systèmes de l'entreprise (ERP, automates, CNC). Cette approche est particulièrement pertinente dans un contexte de production anarchique et changeant, influencé par un taux important de non-qualité. Les travaux d'El Haouzi et Klein sur la conception et l'intégration de SCP, ainsi que les recherches sur les systèmes holoniques de Van Brussel et al., sont mentionnés comme fondamentaux pour cette approche. L'utilisation de technologies infotroniques, notamment la RFID, est envisagée pour permettre une traçabilité simple et sécurisée des produits le long de la chaîne logistique, favorisant une meilleure adaptabilité et flexibilité aux contraintes actuelles. L'objectif est de remplacer les systèmes de contrôle centralisés par un contrôle réactif et distribué.
2. Optimisation de l Ordonnancement avec les Containers Intelligents
Face aux difficultés posées par les boucles de production et les reprises fréquentes, la thèse propose l'utilisation de « containers intelligents ». Plutôt que de suivre chaque pièce individuellement, l'approche privilégie le suivi de groupes de pièces similaires (même gamme de fabrication) regroupées dans des containers. Ces containers, équipés d'un identifiant (code-barres 2D), communiquent des informations cruciales, telles que la date de livraison et le degré d'urgence, au système d'ordonnancement. Cette approche simplifie la gestion des flux, permettant l'utilisation d'un algorithme de programmation linéaire pour l'ordonnancement, qui est beaucoup plus performant pour un nombre réduit de lots. Pour un nombre plus important de lots, un système de basculement vers des algorithmes plus simples est proposé, en fonction de l'état de saturation de l'atelier. Cette gestion est facilitée par une cartographie visuelle des indicateurs clés, simplifiant le pilotage et fournissant une information claire sur l'état de l'atelier.
3. Cartographie Visuelle et Règles de Pilotage
L'analyse des flux de production et de leur perturbation est réalisée à l'aide d'une cartographie visuelle en deux dimensions. Chaque axe représente un indicateur clé: l'un reflète le taux de non-qualité, l'autre la perturbation des flux. Cette représentation permet d'identifier des zones de saturation du système et de déterminer la règle de pilotage la plus appropriée (FIFO, SPT, EDD) en fonction de l'état de l'atelier. Bien qu'elle ne fournisse pas toujours la règle optimale de manière automatique, la cartographie offre une simplification du pilotage, une meilleure compréhension de l'état de l'atelier pour tous les utilisateurs, et une homogénéisation de la gestion sur toute l'unité de production. La recherche d'un équilibre entre un système optimal et un système robuste face à des paramètres souvent incontrôlables est explicitement identifiée comme l'enjeu principal.
IV.Application Industrielle et Résultats
L'implémentation chez Acta-Mobilier a consisté à développer un système de prévision de la non-qualité utilisant les réseaux de neurones pour le robot de laquage. L'analyse des résultats, via des plans d'expériences, a permis d'identifier les paramètres influents sur la qualité. L'utilisation d'ensembles de classificateurs améliore la précision des prédictions. L'intégration de containers intelligents et d'un système de ré-ordonnancement dynamique, basé sur un algorithme simple et efficace, a simplifié le pilotage des flux. Des améliorations organisationnelles, comme l'utilisation de douchettes pour l'identification rapide des lots, ont également contribué à une amélioration significative de l'efficacité globale. Des perspectives futures incluent une meilleure intégration des technologies infotroniques pour une traçabilité encore plus précise.
1. Prévision de la Non Qualité par Réseaux de Neurones
L'implémentation du système de prévision de la non-qualité, au niveau du robot de laquage, a permis de réduire la production de défauts. Des réseaux de neurones ont été entraînés pour prédire l'apparition de défauts spécifiques en fonction des paramètres de production et environnementaux. L'utilisation de réseaux de neurones a permis de mettre en évidence des facteurs influents et des interactions insoupçonnées, là où les experts avaient échoué. L'analyse des résultats, obtenus à l'aide de plans d'expériences, a montré l'impact de paramètres tels que le grammage et le temps de séchage sur l'apparition de défauts. Cependant, certains défauts, notamment ceux liés au comportement des opérateurs (coups), restent difficiles à prédire avec fiabilité, même avec des systèmes d'apprentissage élaborés. Ces défauts constituent une « non-qualité résiduelle » nécessitant d'autres approches que la prédiction par réseaux de neurones. L'utilisation d'ensembles de classificateurs est explorée pour améliorer la précision des prédictions par rapport à un seul classificateur.
2. Optimisation du Flux et Amélioration Organisationnelle
La simplification des flux de production, obtenue grâce aux améliorations apportées, a facilité le pilotage. L’outil POTER, bien que ses premières fonctionnalités aient été centrées sur la traçabilité et l'accès à l'information, a également contribué à l'amélioration du pilotage. Des améliorations organisationnelles ont été mises en place, notamment l'utilisation d'ordres de fabrication uniques par lot avec code-barres 2D, le déploiement de douchettes pour une identification rapide des lots et la déclaration automatique d'anomalies. Ces mesures ont entraîné une amélioration organisationnelle significative, réduisant le temps consacré à l'identification et à la recherche de pièces. L'identification automatique des lots par code-barres 2D est en cours d'implémentation, et l'objectif est de récupérer un maximum d'informations automatiquement (surface des pièces, quantité de laque utilisée) pour optimiser le suivi de production. Le choix entre un simple classificateur et un ensemble de classificateurs dépendra du type de défaut considéré.
3. Règles de Pilotage et Adaptation au Terrain
L'étude a comparé l'efficacité de différentes règles de pilotage (FIFO, EDD, SPT) en fonction du taux de reprises et de l'état de saturation de l'atelier. D'un point de vue opérateur, FIFO est la règle la plus facile à mettre en œuvre. EDD est également simple à appliquer si les dates de départ sont clairement indiquées. SPT, en revanche, nécessite un système d'information performant pour accéder aux temps de traitement de tous les lots, ce qui est plus complexe. L’étude mentionne l'intérêt potentiel d'intégrer cette information directement sur le produit/lot lui-même grâce à des technologies Auto-ID. L'implémentation du système d'ordonnancement est basée sur un système de basculement entre un programme linéaire (pour un faible nombre de lots) et un panel d'algorithmes plus simples (pour un nombre de lots plus important). Ce système permet d'adapter les approches en fonction de la complexité du contexte.